Basic Info.
Model NO.
WE67K-600T/6000
Type
Press Brake
Model
We67K-600t/6000
Type for Bending Hydraulic
Hydraulic CNC
Voltage
as Customer Requirement
Color
Optional
Timely Delivery
About 15 to 25 Days
Place of Origin
Jiangsu, China(Mainland)
Brand Name
Sinomec or OEM
Quality Gurantee
2 Years
Application
Machinery & Hardware
Type for Cutting Machine
Hydraulic Cutting Machine
Type for Fold-Bending Machine
Hydraulic Fold-Bend Machine
Transport Package
Standard
Specification
CE, ISO
Trademark
Sinomec or OEM
Origin
Jiangsu, China
HS Code
8462219000
Production Capacity
2000set/Year
Product Description
Features of CNC Synchronic Press Brake:
1. The electric and hydraulic servo system can control the synchronization of two cylinders. Combined with optical curtain of international standard, the fully closed loop control is formed with high synchronization control accuracy, and high bending and repetitive positioning accuracy.
2. The CNC cylinder deflection auto compensation system helps to prevent the deformed sliding block from affecting the work piece quality and ensure its good linearity and bending angle. The compensation is adjusted automatically by the CNC system, both convenient and accurate.
3. The full functional back gauge system can be extended up to six axes. The work piece can be bent at whatever angled. After welding, the body is machined with the fixture installed only one time. It is processed by CNC pentahedron machining center, ensuring high rigidity and processing accuracy.
4. The hydraulic system adopts the integrated one, which helps to reduce piping connection, eliminate oil leakage, improve the work stability, and beautify the machine appearance. The inner engaged gear pump manufactured by a famous German company is used to reduce the system noise and extend the service life.
5. The die sections have different lengths, which can be combined with a certain width to meet the processing requirements of special work pieces.
6. The upper die hydraulic automatic fastener or quick fastener and plug-in lower die can be equipped based on the customer requirement to reduce work load and improve productivity.
7. The CNC systems are top brand Holland Delem DA52S,DA58T and DA66T. It also features the most advanced electronic board, intelligent modular structure, built-in PLC function, automatic programming and bending simulation, all around shock inspection, remote diagnosis, high resolution color TFT display and Chinese menu.
8. The linear guide, ball and lead screw are German Rexroth and BLIS products, ensuring the positioning accuracy of the machine.
Main Import of Deployment List----WE67K Series
1). Control System: Netherland DELEM, Swiss CYBELEC or Italy ESA.
2). Hydraulic System: Germany HOERBIGER or Rexroth
3). Servo motor and drive: Japanese YASKAWA
4). Raster Ruler: Germany HEIDENHAIN
5). Ball Bearing Lead Screw: Taiwan HIWIN
6). Straight-line Guide: Taiwan HIWIN
7). Seal Ring: FLETZ, Japanese NOK or VALQUA
1. The electric and hydraulic servo system can control the synchronization of two cylinders. Combined with optical curtain of international standard, the fully closed loop control is formed with high synchronization control accuracy, and high bending and repetitive positioning accuracy.
2. The CNC cylinder deflection auto compensation system helps to prevent the deformed sliding block from affecting the work piece quality and ensure its good linearity and bending angle. The compensation is adjusted automatically by the CNC system, both convenient and accurate.
3. The full functional back gauge system can be extended up to six axes. The work piece can be bent at whatever angled. After welding, the body is machined with the fixture installed only one time. It is processed by CNC pentahedron machining center, ensuring high rigidity and processing accuracy.
4. The hydraulic system adopts the integrated one, which helps to reduce piping connection, eliminate oil leakage, improve the work stability, and beautify the machine appearance. The inner engaged gear pump manufactured by a famous German company is used to reduce the system noise and extend the service life.
5. The die sections have different lengths, which can be combined with a certain width to meet the processing requirements of special work pieces.
6. The upper die hydraulic automatic fastener or quick fastener and plug-in lower die can be equipped based on the customer requirement to reduce work load and improve productivity.
7. The CNC systems are top brand Holland Delem DA52S,DA58T and DA66T. It also features the most advanced electronic board, intelligent modular structure, built-in PLC function, automatic programming and bending simulation, all around shock inspection, remote diagnosis, high resolution color TFT display and Chinese menu.
8. The linear guide, ball and lead screw are German Rexroth and BLIS products, ensuring the positioning accuracy of the machine.
Main Import of Deployment List----WE67K Series
1). Control System: Netherland DELEM, Swiss CYBELEC or Italy ESA.
2). Hydraulic System: Germany HOERBIGER or Rexroth
3). Servo motor and drive: Japanese YASKAWA
4). Raster Ruler: Germany HEIDENHAIN
5). Ball Bearing Lead Screw: Taiwan HIWIN
6). Straight-line Guide: Taiwan HIWIN
7). Seal Ring: FLETZ, Japanese NOK or VALQUA
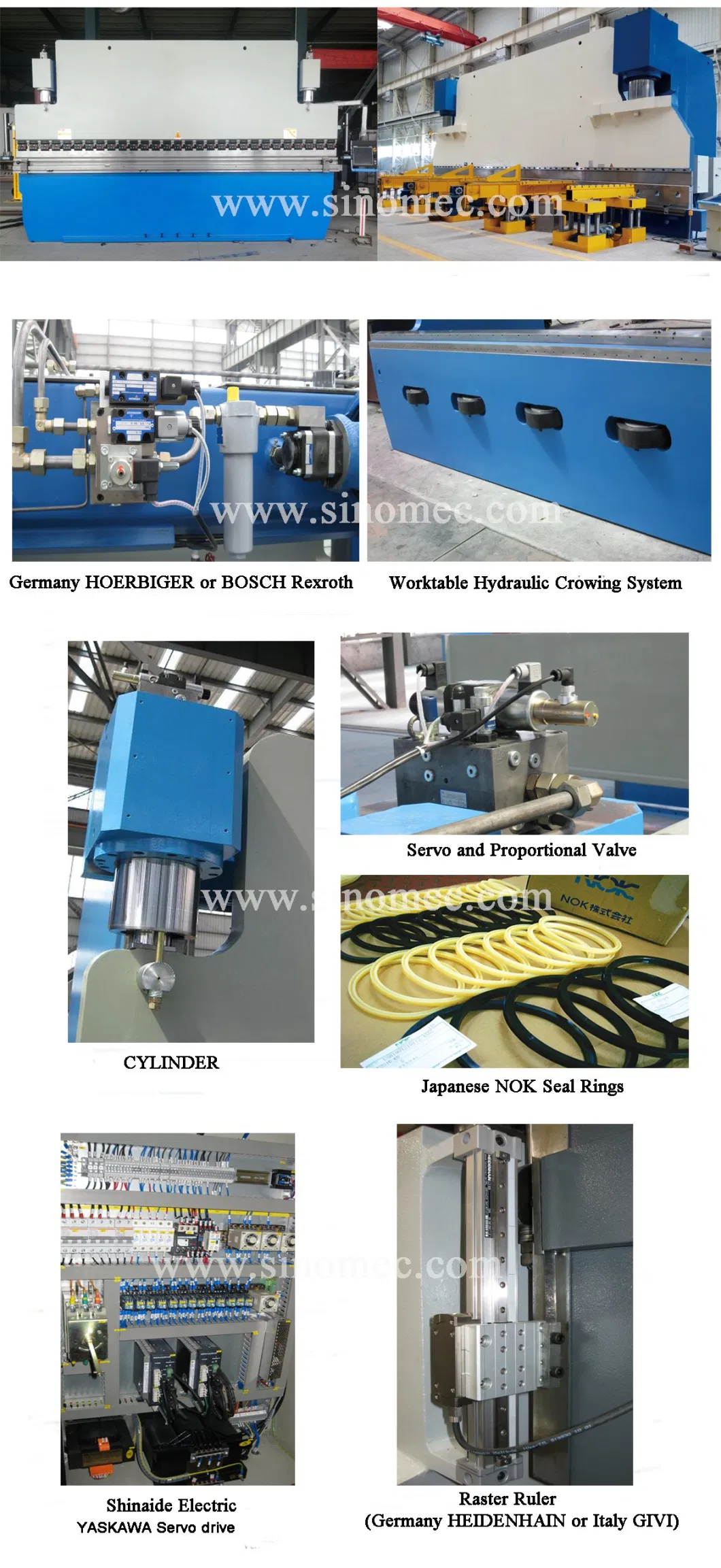
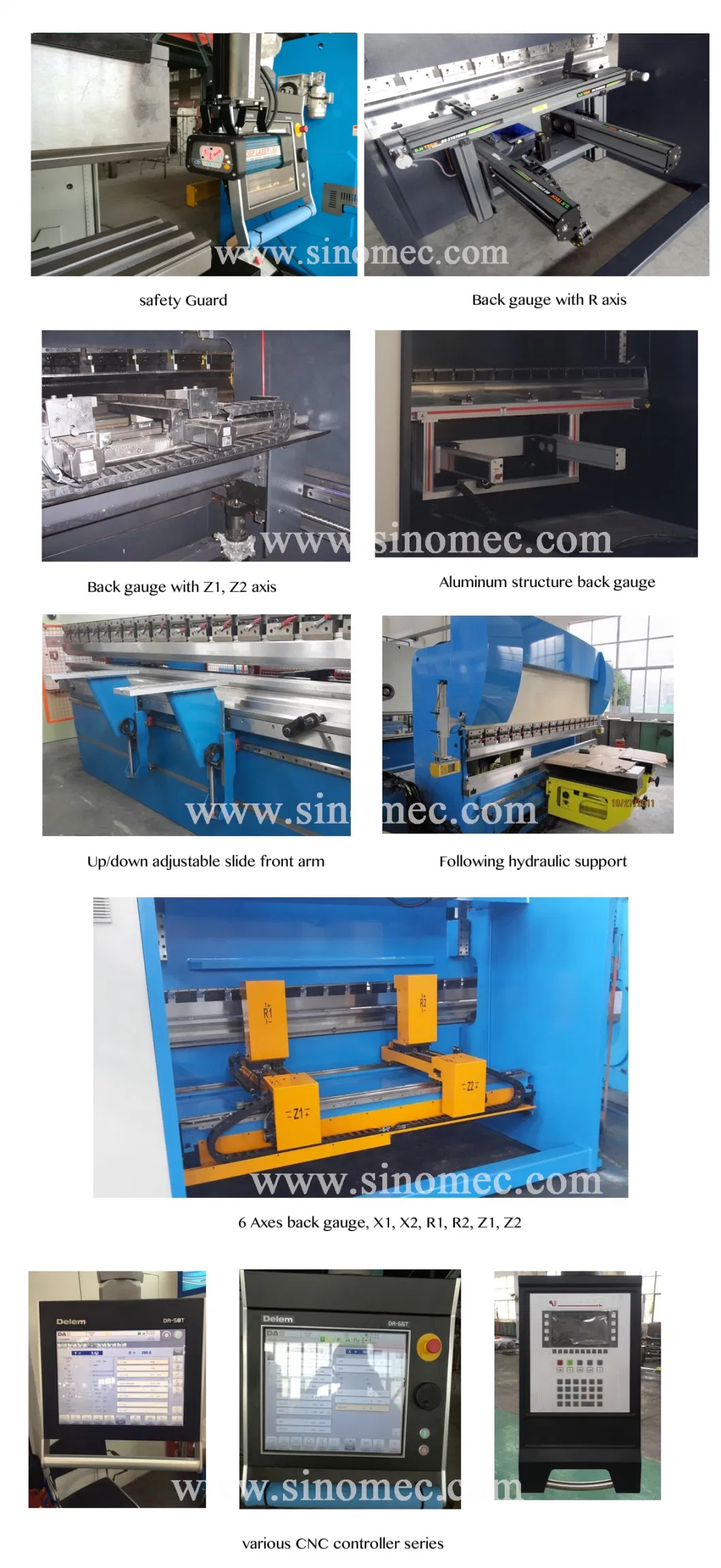
Technical Parameters | ||||||||||
Model | 40T/2500 | 50T/2500 | 63T/2500 | 80T/2500 | 80T/3200 | 80T/4000 | 100T/3200 | 100T/4000 | 125T/3200 | 125T/4000 |
Bending Force (KN) | 400 | 500 | 630 | 800 | 800 | 800 | 1000 | 1000 | 1250 | 1250 |
Bending Length (mm) | 2500 | 2500 | 2500 | 2500 | 3200 | 4000 | 3200 | 4000 | 3200 | 4000 |
Vertical Distance (mm) | 1900 | 1900 | 1900 | 1900 | 2700 | 3500 | 2700 | 3500 | 2700 | 3500 |
Throat Depth (mm) | 300 | 300 | 350 | 350 | 350 | 350 | 400 | 400 | 400 | 400 |
Stroke (mm) | 150 | 150 | 170 | 170 | 170 | 170 | 200 | 200 | 200 | 200 |
Worktable Height (mm) | 800 | 800 | 800 | 800 | 800 | 800 | 800 | 800 | 800 | 800 |
Worktable Width (mm) | 320 | 350 | 380 | 380 | 380 | 380 | 420 | 420 | 420 | 420 |
Quick down speed (mm/s) | 120 | 120 | 120 | 120 | 120 | 120 | 120 | 120 | 120 | 120 |
Return Speed (mm/s) | 100 | 100 | 100 | 110 | 110 | 110 | 100 | 100 | 100 | 100 |
Working speed (mm/s) | 10 | 10 | 10 | 10 | 10 | 10 | 10 | 10 | 10 | 10 |
Back gauge stroke (mm) | 500 | 500 | 500 | 500 | 500 | 500 | 500 | 500 | 500 | 500 |
Back gauge speed (mm/s) | 200 | 200 | 200 | 200 | 200 | 200 | 200 | 200 | 200 | 200 |
Main power (Kw) | 5.5 | 5.5 | 5.5 | 7.5 | 7.5 | 7.5 | 7.5 | 7.5 | 11 | 11 |
No. of Axis (4+1) | Y1, Y2, X, R, Hydraulic crowning table | |||||||||
Weight(Approx.) (Tons) | 3.5 | 4.5 | 5.8 | 7 | 7.8 | 8.5 | 8.5 | 9.5 | 9 | 9.8 |
Model | 160T/3200 | 160T/4000 | 160T/6000 | 200T/3200 | 200T/4000 | 300T/3200 | 300T/4000 | 400T/4000 | 400T/6000 | 500T/6000 |
Bending Force (KN) | 1600 | 1600 | 1600 | 2000 | 2000 | 3000 | 3000 | 4000 | 4000 | 5000 |
Bending Length (mm) | 3200 | 4000 | 6000 | 3200 | 4000 | 3200 | 4000 | 4000 | 6000 | 6000 |
Vertical Distance (mm) | 2700 | 3500 | 4900 | 2700 | 3500 | 2700 | 3500 | 3500 | 4900 | 4900 |
Throat Depth (mm) | 400 | 400 | 400 | 400 | 400 | 400 | 400 | 400 | 400 | 500 |
Stroke (mm) | 200 | 200 | 200 | 200 | 200 | 200 | 200 | 200 | 200 | 320 |
Worktable Height (mm) | 800 | 800 | 800 | 800 | 800 | 800 | 800 | 800 | 800 | 800 |
Worktable Width (mm) | 80 | 80 | 80 | 100 | 100 | 100 | 100 | 110 | 110 | 300 |
Quick down speed (mm/s) | 120 | 120 | 120 | 120 | 120 | 120 | 120 | 110 | 110 | 85 |
Return Speed (mm/s) | 100 | 100 | 100 | 100 | 100 | 110 | 110 | 80 | 80 | 75 |
Working speed (mm/s) | 10 | 10 | 10 | 10 | 10 | 10 | 10 | 10 | 10 | 8 |
Back gauge stroke (mm) | 500 | 500 | 500 | 500 | 500 | 500 | 500 | 500 | 500 | 500 |
Back gauge speed (mm/s) | 200 | 200 | 200 | 200 | 200 | 200 | 200 | 200 | 200 | 200 |
Main power (Kw) | 11 | 11 | 15 | 15 | 15 | 18.5 | 18.5 | 22.5 | 30 | 37 |
No. of Axis (4+1) | Y1, Y2, X, R, Hydraulic crowning table | |||||||||
Weight(Approx.) (Tons) | 11 | 12 | 19.5 | 14.2 | 15.5 | 16.8 | 18 | 31 | 35 | 53 |